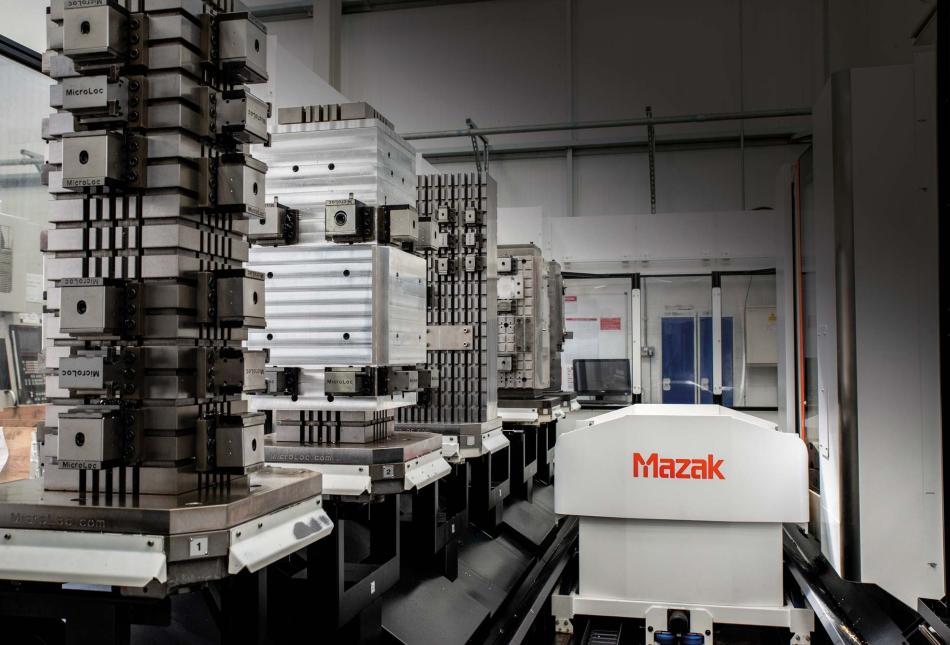
Our recent venture into a long-term project for our CNC machining department has illuminated the critical importance of enhancing production efficiency. Through meticulous assessment, strategic investments, and continuous optimisation efforts, The Continuous Improvement Team, here at Portsmouth Aviation achieved remarkable results that underscore our commitment to innovation here at Portsmouth Aviation. By investing in new technology, they achieved a drastic reduction in operation time and waste, something that has made a difference in terms of our productivity, sustainability, and delivery time for the customer.
The first stage of this new approach to machining was assessment and analysis. Understanding the intricacies of their project's requirements was the first step towards success. They analysed factors such as tolerances, material properties, and production volumes to tailor our approach accordingly. From their findings, they made a strategic decision to invest in the Mazak HNC 5000 twin pallet machine. This cutting-edge equipment not only met their immediate needs but also positioned us for future growth and versatility as a company.
Once purchasing the new technology, they entered the initial production phase. As they embarked on machining the crucial components, they encountered challenges that demanded swift action. Identifying areas for improvement in run time and setup efficiency propelled them towards optimisation. The team took on this change in approach with the knowledge they would encounter challenges, and it was up to our dedicated team to utilise their extensive knowledge to tackle them.
Implementing optimisation strategies was imperative to success. Transitioning to extrusions and introducing new clamping methods significantly enhanced efficiency while reducing waste and setup time. The implementation of these strategies led to integrate cutting-edge tools from ISCAR Tooling, elevating standards of precision and efficiency to new heights.
Buoyed by the initial success of the project, the CNC department ventured further by investing in the Mazak Palletech System, enabling them to scale operations with unmatched efficiency and minimal downtime. Integrating automation and precision tools such as the Renishaw Probe ensured consistent quality and minimised deviations, further bolstering our reputation for excellence.
What was key to this change, was the investments in technologies like the swarf compactor, optimising the processes for lights-out running and reduced manual intervention. The journey culminated in the establishment of a self-contained production cell, something that has made a significant difference to our staff, and the customer. Based on studies over two jobs, in which we compared the previous process to the new, we concluded that the time spent went from 6 hours to just 2 and a half, in both cases. The reduction in waste and use of the swarf compactor has also had a significant impact on our sustainability efforts.
Innovation and continuous improvement are the hallmarks of our journey. Through strategic investments, relentless optimisation efforts, and a steadfast commitment to excellence, our fantastic team at Portsmouth Aviation have revolutionised production efficiency and quality standards. This case study is a testament to our unwavering dedication to meeting the evolving needs of our projects and customers. As we march forward, we remain steadfast in our pursuit of excellence, shaping the future of engineering with every endeavour.
To learn more about the work our CNC machining team is doing, head over to their page! If you’d like to speak to someone further about what Portsmouth Aviation’s CNC Machining department can do for you, contact manager Andy Freemantle or reach out via our contact us page. We look forward to hearing from you in how Portsmouth Aviation can engineer your vision.